Fleet managements and OEMs are increasing concerned with seat technology to increase driver comfort, health and safety. Carbon Air products demonstrate clear and objective performance benefits in seat technology. Carbon Air technology, through a process called sorption, controls the behaviour of gasses. When this is applied to a seat air spring the effects are radical.
Benefits
Driver Comfort
NVH and comfort have a significant impact on driver fatigue and health, which in turn affects downtime and operating efficiencies – as highlighted by the Truckload Carriers Association (TCA). A cab seat air spring with Carbon Air technology offers unrivalled comfort, by lowering the stiffness beyond what is possible by any other means alone. This means a reduction in vibrations transmitted from the cab to the driver and with it the potential to reduce driver fatigue and downtime.
Packaging
Carbon Air products, through adsorption, increase the pneumatic volume without increasing the physical volume of the container. This effect offers an entirely new design dimension, and one of the more obvious possibilities is downsizing the air spring, given ever-present packaging constraints.
Adjustability
Carbon Air products can be used to adjust the behaviour of an existing seat assembly. The quantity of treatment allows one to modify the behaviour of any given seat and air spring product assembly without the need to develop new hardware.
Dyno Testing
At the heart of a cab seat performance is the air spring. The effect of Carbon Air technology on seat air springs was measured at our inhouse testing facilities.
A typical seat air spring was tested untreated and again with treatment by Carbon Air. Comparisons were made with two tests, both performed on a Mechatronics Labs dyno with Carbon Air’s inhouse developed control and post processing. The first test used a dynamic input with a deflection of 50mm (ie +/-25mm) at 2Hz. This was conducted at 2bar, 3bar, 4bar, 5bar and 6bar (where the 3bar is of primary concern given it best represents typical in duty operation). Pressure was set at the point of peak extension within the 50mm displacement. The second test used a dynamic input with a deflection on 25mm at 2Hz. The same pressure range and procedure was used. The second test was used only to produce single stiffness values for the air spring at the displacement midpoint.
Results
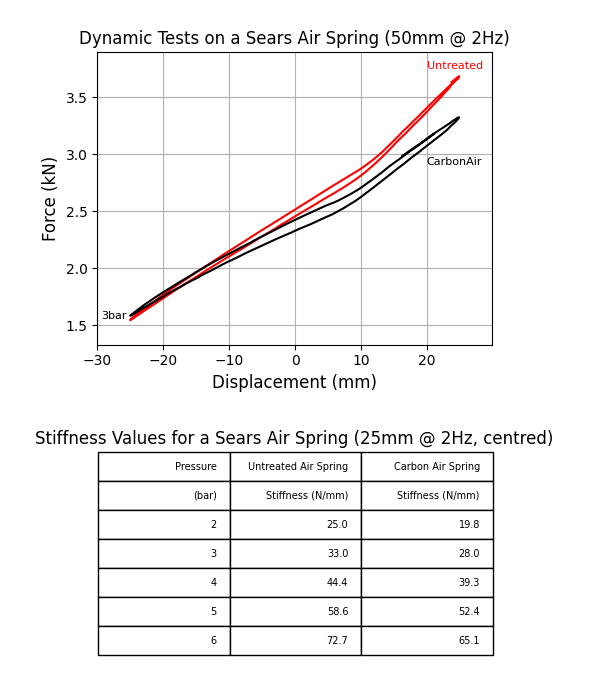
The results show a 15% reduction in stiffness. But what does this mean in practice? A driver sat on the same seat and spring assembly, setting the air pressure to achieve the same seat position, will be isolated from significantly more vibration. With a minimal hardware change, driver comfort is suddenly improved.