This paper details the benefits of using Carbon Air activated carbon inserts in automotive air suspension systems, with a focus on rolling lobe air springs.
Overview
Suspension systems have a number of functions. They are primarily used to support the weight of a vehicle, ensure consistent contact with the road, and absorb impacts and attenuate the roughness of a road profile; this leads to improved handling, stability, reduced wear and increased rider comfort. Suspensions have a range of allowable motion: this is the amount of travel or their stroke length. Air springs are often chosen for their ride comfort and adaptability: by altering the line pressure on the fly, a vehicle can quickly adapt to different loads and terrains. However, the behaviour of air and a number of size and other engineering constraints can leave little space to improve performance.
The advantages of Carbon Air products
Carbon Air technology, through a process called sorption, controls the behaviour of gasses. Our products for air springs reduce the stiffness of an air chamber without affecting its geometry or pressure in any way. The three main benefits of the effect are comfort, downsizing and tunability.
Comfort
Conventional air springs will always hit hard limits when striving for ride comfort – limits relating to packaging, wheel travel, air spring geometry and static load-bearing. An air spring with Carbon Air products offers unrivalled ride comfort, by lowering the stiffness beyond what is possible at a given pressure, load and size. This translates in reduced vibrations transmitted from wheels to passengers. The thermodynamics of air also dictate that air springs must be stiffer in fast motions than in slow ones, as pressure is higher when extra heat is not allowed enough time to escape the gas. Carbon Air products, through their high surface area, mitigate this effect by ensuring that heat is quickly dissipated away from the gas, resulting in a more consistent low stiffness between slow and fast motions.
Downsizing
Carbon Air products, through adsorption, increase the pneumatic volume without increasing the physical volume. This effect offers an entirely new design dimension, and one of the more obvious possibilities is downsizing the air spring, given ever-present packaging constraints.
Tunability
Carbon Air products can be used to adjust and tune the behaviour of an existing air suspension to meet performance targets. The quantity of treatment allows one to modify the behaviour of any given air cavity in incremental steps until it achieves the desired characteristic. At the later stages of vehicle development, when many attributes and hardwares have been frozen, Carbon Air brings scope for further tweaking of a vehicle’s dynamic characteristics. At the earlier stages of vehicle development, Carbon Air brings scope for the homogenisation of suspension hardware across multiple trim levels, and even multiple vehicle platforms.
Air Springs
An automotive air spring usually consists of a flexible sleeve (typically reinforced rubber) mounted between two plates (or a plate and a piston). The assembly forms a sealed air cavity that is commonly pressurised to around 6 bar. There are two main types of air spring designs: “rolling lobe”, where a single sleeve rolls over a piston in compression, and “convoluted”, with a number of bellows that splay outwards. A rolling lobe type air spring (our case study for Carbon Air products) is shown in Figure 1. All air springs operate on the same principle: the spring force is primarily determined by the gas pressure.
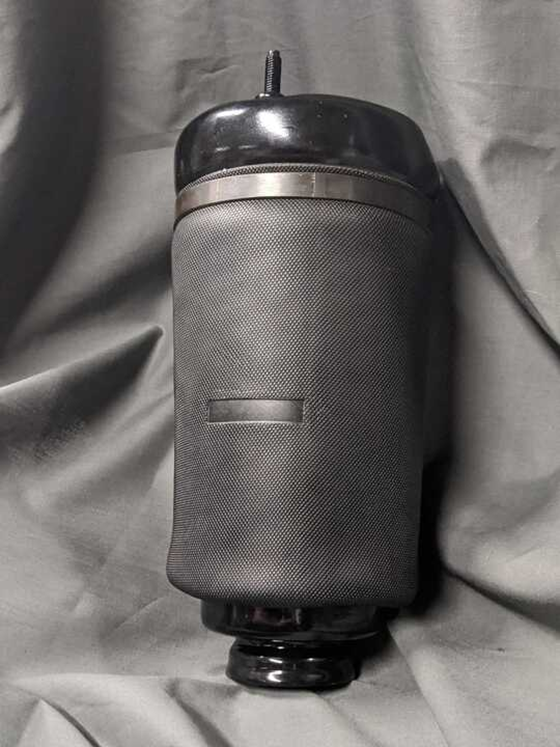
The characteristics of the spring are affected by the charge pressure, the air volume, the profile of the piston and the effective surface area over which the gas pressure is distributed. By moving the piston, the air in the main chamber is compressed, and so the pressure increases, causing a higher spring force. Very little damping occurs inside the air cavity, with most of the input energy being stored by the spring. For this reason, these suspensions generally require a separate damper in parallel to dissipate the energy from the road profile. Compared to coil springs that have a more constant stiffness through travel, air springs are naturally progressive, i.e. their stiffness increases with travel. Air springs are also sensitive to temperature changes, as temperature increases cause increases in pressure. A measured static spring force curve is shown in Figure 2. Notice: steeply increasing force at higher displacements (progressivity), and a slightly flatter region around 60mm, near the ride height, due to the piston inwards shape. The stiffness is also dependent on the speed of compression/extension, because of the thermodynamics of gases: faster compressions cause higher pressure peaks than slower ones because additional heat accumulated by compressing the gas is not allowed enough time to escape. Figure 3 shows dynamic force curves over 50 mm travel at different speeds (25 and 400 mm/s). It shows that higher speeds result in a higher peak force and an overall stiffer spring.
Air spring design
An air spring design is arrived at by balancing a large number of concerns, including: packaging, wheel travel, ride height, static load-bearing and comfort. Modifications to the geometry, material, and pressure affect the spring rate in different ways, and each have their benefits and drawbacks. Increasing pressure makes the spring stiffer and allows a heavier load (and vice-versa). Changing the profile of the piston can make the stiffness more or less progressive through the course of travel. Increasing the volume affects both progressivity and stiffness: a larger volume decreases the stiffness for a given pressure and makes the spring curve more linear. In a real application, a heavy load might require a higher pressure and greater piston surface area. The resulting high spring force at ride height will mean a harsher ride. A larger volume can reduce the stiffness but is limited by the overall vehicle height, structure and other components. With these constraints, it is hard to design a spring that is both comfortable and can accommodate the load appropriately. The properties of gas in a cavity are considered a constant. But what if you could change the behaviour of air? This is where sorption comes into play, the key ingredient to Carbon Air suspension products.
Carbon Air technology
Adsorption mechanism
Activated carbon, like other sorptive materials, has the property of trapping (adsorbing) molecules to its surface, through the action of van der Waals forces. Thanks to its high surface area (over a thousand square metres per gram) provided by a network of pores, activated carbon can adsorb a large amount of gas, which forms a film on the solid surface, removing it from the gas phase. The amount of gas adsorbed increases or decreases based on the gas pressure. An isotherm of one of our activated carbons is shown in Figure 5, where the amount of gas (nitrogen) adsorbed per gram of carbon is plotted against pressure.
In an air suspension with such material, the pressure curve of the chamber is dramatically altered. An increase in pressure during compression causes gas to be trapped by the material, while a drop in pressure from extension causes some of the trapped gas to be released from the surface (desorbed). What this means is that the changes in pressure with compression and extension are counteracted by adsorption/desorption, and so are less dramatic than what they would otherwise be. As a result, the air suspension behaves as if it had a larger volume, with a lower resulting stiffness! Each unit of volume occupied by our activated carbon is roughly doubled, though the effect varies based on the variety chosen and the operating pressure, with the strongest effect found at lower pressures. For example, a 1.5 litre chamber can be made to behave as a 2 litre chamber with a 500 ml insert. This may be counter to intuition – and why would filling a cavity with solid material make it behave as if it had more volume and not less? – but results in the next section show the effect is real, and can be put to good use.
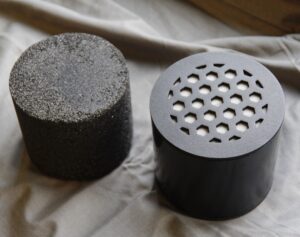
Tested benefits
The measurements carried out in our laboratory demonstrate each of the three major advantages of using Carbon Air activated carbon products in an automotive air spring: comfort, downsizing and tunability. In our case study, an air spring was chosen from a luxury passenger vehicle, and is shown in figure 7. With a charge pressure of 6 bar, the initial spring force is around 500 kg. The spring underwent static and dynamic compressions up to 180 mm to demonstrate the effects of activated carbon.
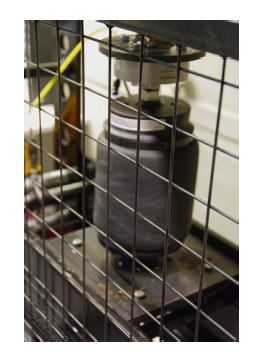
Comfort
Figure 8 shows the stiffness of the air spring in response to small perturbations of 5 mm around the nominal ride height at frequencies between 0.01 and 4 Hz. These oscillations are of the same order as a road profile. The Carbon Air spring is significantly more compliant than the original spring throughout the whole frequency range from very slow motions at slow speed (1 cycle every one hundred seconds) to rapid vibrations at 10 cycles per second, while the starting pressure and static force are the same as for the untreated spring. A lower stiffness around the ride height results in increased rider comfort as the spring can be more easily compressed in response to the road profile, reducing the transmission of unwanted vibrations from the wheels to the passengers. The high surface area of activated carbon serves a dual function: not only does it help to lower the peak pressure during impacts by trapping air molecules, but also acts as a heat exchanger, to dissipate the additional heat build-up in compression quickly, reducing the contrast between slow and fast compressions. When air is compressed, its temperature increases as well as its pressure. If the compression is slow enough, the extra heat is passed to the outside, which in turn lowers the pressure of the gas. What this means is that for slow compressions, the air pressure is not as high as for fast compressions. This results in higher stiffness when it’s least wanted: for large and rapid impacts. The frequency sweep in figure 8 shows how the untreated spring has not only a higher stiffness, but also a greater contrast between slow and fast motions. Additionally, the effect can be seen over a large pulse, shown in figure 10 the spring was compressed by the same amounts at two different speeds: 25 and 400 mm/s. The untreated spring has a 500 N additional force at the end stroke when compressed quickly.
Downsizing
A given air spring can be tuned to behave like a larger air spring. This can be seen by the relative linearity (the increase in force is less steep, particularly towards high displacements) normally associated with a larger unswept air volume (as shown in figure 9), and with the lower stiffness measured in the frequency plot in figure 8: the measured drop from 80 to 55 N/mm equates to a 45% increase in effective air spring dynamic volume. At 33% volume fill (300 grams in this spring), it means every litre of carbon adds around 1.4 litres to the dynamic volume.
Equivalently, a smaller air spring could be used to do the job of a larger predecessor. The desired spring progression, a product of the swept and unswept air volumes, can be replicated with a physically smaller unswept volume, reducing the overall dimensions of the air spring. The downsizing afforded by Carbon Air technologies is not limited to the airspings themselves, but the entire suspension system. Air tanks and accumulators can also benefit from increased capacity and/or reduced dimensions. The challenges of vehicle packaging are more demanding than ever. BEVs and autonomous vehicles have ushered in a thorough re-evaluation of vehicle layouts in general. For example, uptake of wheel modules will be reliant upon the expected standard of vehicle dynamics being met, despite the tremendous packaging constraints. Carbon Air technology will only become increasingly critical.
Tunability
Activated carbon inserts can be made to make incremental and fine adjustments to an air spring. Figure 11 shows that different quantities of activated carbon allow selecting a desired response of the same spring from a wide range of possibilities. This gives scope to enhance and tweak the performance of existing and fixed designs by just modifying the behaviour of the air or gas in the cavity.
Summary
Carbon Air activated carbon offers three major benefits to automotive air springs:
- Comfort: decreased stiffness without affecting geometry or pressure, allows a spring to easily compress and adapt to a road profile and minimises transmitted vibrations from wheels to passengers.
- Downsizing: decreased stiffness means a small air volume will perform just the same as a larger one, allowing great space savings and new design possibilities.
- Tunability: The effect of activated carbon scales with the quantity of treatment. This allows the tuning of existing suspension hardware in small increments to achieve a desired response. Such tuning could be fine tweaks at the final stages of vehicle dynamics development. Carbon Air technology could also facilitate a modular system of air suspension components, tailoring spring characteristics for every vehicle sharing cross-platform air spring hardware.